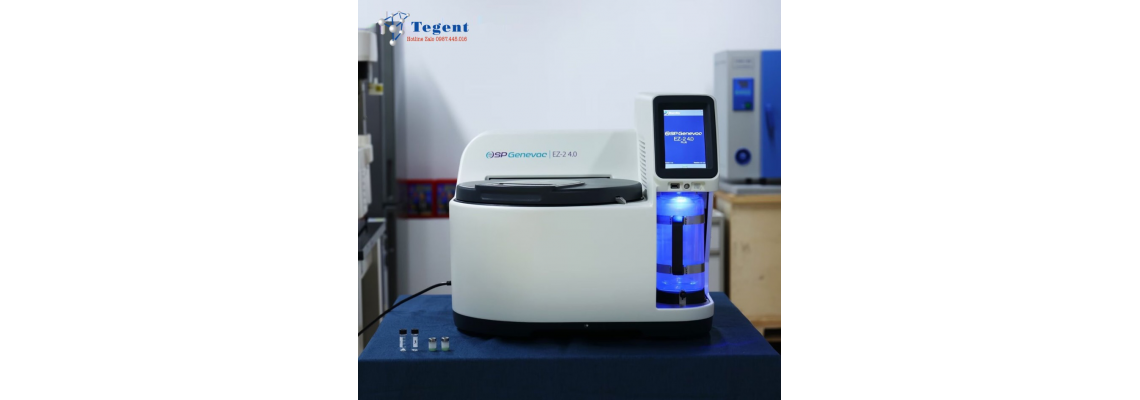
Lựa chọn máy cô dung môi
Thiết bị cô dung môi: là loại thiết bị dùng để cô đặc mẫu hay đuổi dung môi.
Có nhiều phương pháp khác nhau như: máy cô quay chân không, máy cô dung môi nhiều vị trí….
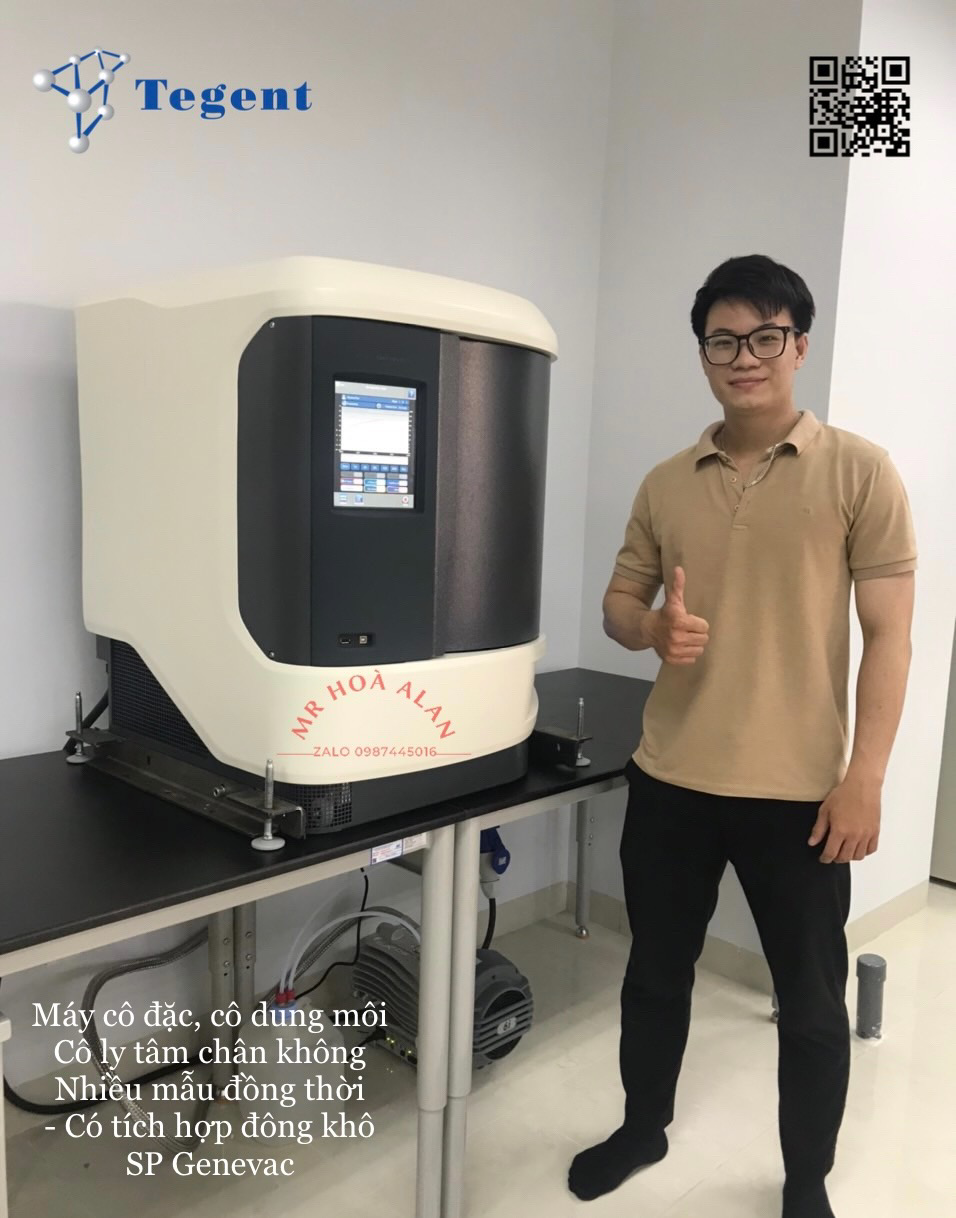
Cô mẫu nhiều vị trí có ly tâm HT Series3i Genevac
Vấn đề cơ bản về lựa chọn máy cô dung môi
Đánh giá đặc tính sản phẩm và yêu cầu quy trình để lựa chọn trong số các thiết kế thiết bị bay hơi khác nhau.
Thiết bị bay hơi được sử dụng trong nhiều quy trình, bao gồm dược phẩm, thực phẩm và đồ uống, bột giấy và giấy, hóa chất, polyme và nhựa, muối vô cơ, axit, bazơ và nhiều loại vật liệu khác. Có nhiều loại và biến thể của thiết bị bay hơi và loại tốt nhất cho một ứng dụng cụ thể phụ thuộc vào đặc tính sản phẩm và kết quả mong muốn.
Bài viết này trước tiên giải thích các yêu cầu của quy trình mà thiết bị bay hơi phải đáp ứng, đồng thời thảo luận về các đặc tính sản phẩm và vận hành quan trọng cũng như ảnh hưởng của chúng đối với việc lựa chọn thiết bị bay hơi. Sau đó, nó xem xét các loại thiết kế thiết bị bay hơi khác nhau, phương thức hoạt động, tính năng, ưu điểm và hạn chế của chúng, đồng thời cung cấp hướng dẫn về cách chọn thiết bị bay hơi cho một ứng dụng cụ thể.
- Bay hơi là một hoạt động được sử dụng để cô đặc dung dịch chất tan không bay hơi và dung môi dễ bay hơi, trong nhiều trường hợp là nước. Một phần dung môi được bay hơi để tạo ra dung dịch đậm đặc, dạng bùn hoặc chất lỏng đặc, nhớt.
- Sự bay hơi khác với quá trình sấy khô ở chỗ cặn là chất lỏng có thể chảy được thay vì chất rắn. Sự bay hơi khác với quá trình chưng cất ở chỗ không có nỗ lực tách hơi thành các thành phần riêng lẻ.
- Hơi hoặc dòng cô đặc, hoặc cả hai, có thể là sản phẩm mong muốn (1). Do đó, thiết bị bay hơi phải được thiết kế để phân tách rõ ràng hơi khỏi nước ngưng và nguồn cấp.
- Thiết bị bay hơi bao gồm một bộ trao đổi nhiệt hoặc bể nước nóng, van, ống góp, bộ điều khiển, máy bơm và bình ngưng. Các thiết kế phổ biến nhất là bể chứa có vỏ bọc, bộ trao đổi nhiệt dạng ống, bộ trao đổi nhiệt dạng tấm và khung và thiết bị bay hơi màng mỏng có khuấy.
LỰA CHỌN MÁY CÔ DUNG MÔI DỰA TRÊN CÁC YẾU TỐ:
- Được thiết kế để truyền nhiệt hiệu quả ở tốc độ cao với diện tích bề mặt tối thiểu để tiết kiệm chi phí cho việc lắp đặt, vận hành và bảo trì
- Tách hơi hiệu quả khỏi chất lỏng cô đặc
- Đáp ứng các điều kiện theo yêu cầu của sản phẩm đang được xử lý
- Tạo ra sản phẩm đạt chất lượng yêu cầu
- Tiết kiệm năng lượng, khi có thể, sử dụng hơi nước một cách hiệu quả với khả năng bay hơi hoặc nén hơi đa hiệu ứng
- Giảm thiểu sự bám bẩn của bề mặt truyền nhiệt
- Được xây dựng bằng vật liệu phù hợp để giảm thiểu sự ăn mòn
- Đặc tính sản phẩm và vận hành quan trọng
Các đặc tính sản phẩm và vận hành quan trọng của dung dịch cô quay có ảnh hưởng lớn đến việc lựa chọn loại thiết bị bay hơi phù hợp nhất cho ứng dụng.
Độ nhạy nhiệt
Nhiều loại thực phẩm, dược phẩm, hóa chất và nhựa nhạy cảm với nhiệt hoặc nhiệt độ và yêu cầu nhiệt độ gia nhiệt thấp hoặc thời gian lưu trú ngắn tiếp xúc với nhiệt hoặc cả hai. Điều này có thể được thực hiện bằng cách kết hợp giảm thiểu thể tích sản phẩm trong thiết bị bay hơi vào bất kỳ lúc nào, giảm thiểu thời gian trong thiết bị bay hơi và giảm nhiệt độ sôi khối của sản phẩm bằng cách vận hành thiết bị bay hơi ở áp suất giảm. Việc giảm áp suất vận hành bên trong cũng có thể cho phép vận hành ở nhiệt độ gia nhiệt thấp hơn trong khi vẫn duy trì lực truyền nhiệt hợp lý (chênh lệch nhiệt độ giữa điểm sôi của sản phẩm số lượng lớn và nhiệt độ của môi trường gia nhiệt).
Làm bẩn
Sự bám bẩn trên bề mặt truyền nhiệt thường do chất rắn trong nguyên liệu, kết tủa chất rắn trong chất cô đặc hoặc sự xuống cấp của sản phẩm. Sự hình thành chậm của màng trên bề mặt truyền nhiệt sẽ làm giảm dần hệ số truyền nhiệt tổng thể. Cuối cùng, điều này sẽ yêu cầu dừng quy trình và làm sạch các bề mặt truyền nhiệt, dẫn đến thời gian ngừng sản xuất và tốn thêm nhân công bảo trì.
Tạo bọt
Sản phẩm tạo bọt trong quá trình hóa hơi là phổ biến. Nó có thể dao động từ một lượng nhỏ bọt không ổn định, dễ vỡ đến bọt rất ổn định, khó vỡ và có xu hướng lấp đầy toàn bộ khoảng trống của hệ thống bay hơi. Việc tạo bọt thường có thể được giảm thiểu bằng các thiết kế đặc biệt cho đầu vào cấp liệu (tách thức ăn khỏi dòng hơi) và khu vực tách hơi/lỏng (thiết kế tách đặc biệt). Ngoài ra, việc giảm cường độ sôi của chất lỏng trên bề mặt truyền nhiệt (bằng cách vận hành ở nhiệt độ thấp hơn hoặc áp suất cao hơn) và giảm tốc độ hơi trong ống có thể làm giảm đáng kể khả năng tạo bọt. Khi các thông số kỹ thuật về độ tinh khiết của sản phẩm cho phép, hãy áp dụng một chất chống tạo bọt có thể giải quyết hoặc làm giảm đáng kể vấn đề.
Chất rắn
Các tính chất của chất cô đặc có thể thay đổi khi nồng độ chất rắn tăng lên. Chất rắn có thể làm tắc ống, gây mất bề mặt truyền nhiệt, dẫn đến tốc độ truyền nhiệt giảm và yêu cầu
Xem chi tiết tại đây
Xem thêm về các sản phẩm cô ly tâm chân không tại đây
Để lại một bình luận